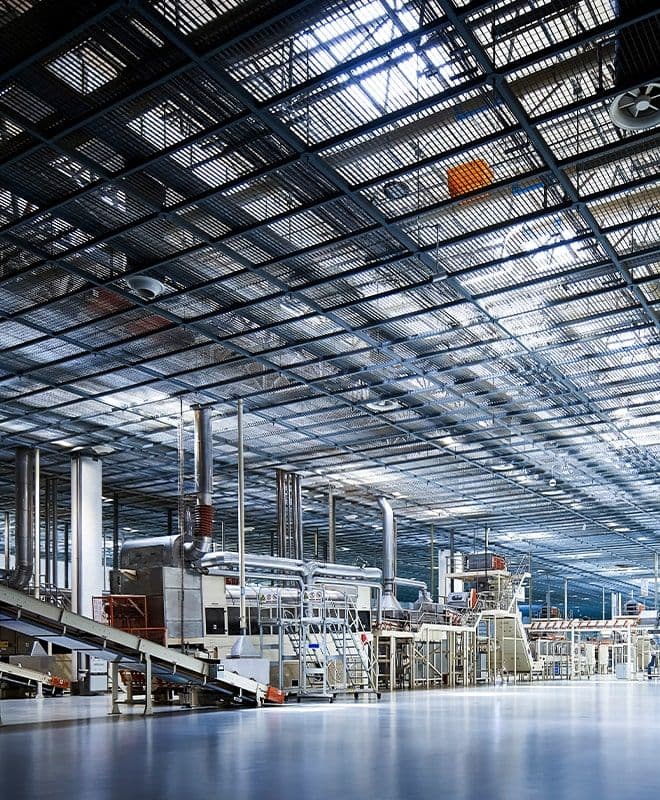
Manufacturing Excellence
Leveraging Technology to provide Custom HVAC Solutions for addressing market demands
Manufacturing Facilities
Blue Star has extensive product testing facilities aimed at enabling the development and manufacturing of high-quality products at our various factories in India.
![]() | Inception: 2007 Location: This factory is 73 km Northeast of Mumbai, India Area: 14,100 sq. m. (151.7K sq. ft.) Products Manufactured: HVAC Chillers, Cold Room Refrigeration Products (Positive & Negative Temperature), Cold Room Refrigeration Panels (Positive & Negative Temperature), Mortuary Chambers, Water Coolers, Deep Freezers, Evaporator and Condensing Units
The strategic location of this Blue Star air conditioning manufacturing facility in Wada near Mumbai, India, positions it to become the largest manufacturing hub. This modern plant deploys cutting-edge systems for quality and efficiency, utilising Lean Manufacturing, Six Sigma, and Kaizen methodologies. Notably, the facility achieved a Platinum-rated IGBC Green Building certification in 2022, underscoring its commitment to sustainable practices. These initiatives include maximising natural light and ventilation, using energy-efficient cooling systems, water conservation measures, and eco-friendly landscaping. Furthermore, as a part of our renewable energy adoption, this facility has added a 2.1 MW Roof Top Solar Plant in April 2023 to the existing 1 MW Plant, augmenting it to a 3.1 MW Roof Top Solar Plant. This recognition highlights Blue Star's dedication to responsible manufacturing and environmental leadership. |
| Inception: January 2023 Location: Sri City, Andhra Pradesh, India Area: 50,000 sq.m. (538.1K sq. ft.) (Once fully built) Products Manufactured: Inverter Mini Split ACs, Cassette ACs
Blue Star's AC manufacturing plant in Sri City near the Chennai Port, India, primarily caters to the South and West market requirements. Its strategic positioning ensures the efficient transportation of products. Additionally, it is positioned to serve overseas demand in Europe and North America through the International Business Group in the future. This state-of-the-art facility boasts cutting-edge machinery with the latest automation techniques and tools, facilitating top-tier manufacturing processes. With a remarkable capacity of 322,000 units in the fiscal year 2024, it aims to scale up to an impressive 1.6 million units within the next five years. The facility also emphasises increased value addition through backward integration while leveraging benefits such as Production Linked Incentives (PLI), income tax benefits, and Manufacturing and Other Operations in Warehouse Regulations (MOOWR) benefits, further enhancing its competitive edge in the global market. |
Inception: 1997 Location: Dadra and Nagar Haveli, a Union Territory 160 km from Mumbai with its capital at Silvassa, India Built-up Area: 12,000 sq. m. (129K sq. ft.) Products Manufactured: VRF Systems, Ducted Inverters, Ducted Split Inverters, Ducted Packaged Units
Blue Star's AC manufacturing plant in Dadra has been built in technical collaboration with Rheem, USA, and exemplifies cutting-edge manufacturing. Recognised as a leading Indian air conditioning hub, it leverages an integrated SAP ERP system for seamless operations. It implements advanced principles like visual factory management, Just-in-Time, Kaizen, and Lean methodologies for ensuring efficient production and minimising errors. Its highly integrated assembly line boasts strong backward integration with coil shops, fabrication shop, paint shops and powder coating shop, enabling the production of a diverse portfolio including ducted & ducted inverter units, inverter VRF ACs, and more. This facility showcases Blue Star's commitment to innovation and efficiency in air conditioning manufacturing. |
![]() | Inception: 2005 Location: This factory is 300 km Northwest of North Delhi, India
The industrial zone of Kala Amb in the Solan district of Himachal Pradesh, India, has seen a proliferation of manufacturing setups in the recent past. Our AC manufacturing plant has successfully capitalised on this opportunity to augment its manufacturing capabilities. This factory has been set up in the sylvan settings of Kala Amb, India. It is a highly productive, automated, and flexible unit that manufactures outdoor and indoor units of split air conditioners coupled with a fin and tube heat exchangers (FTHX) coil manufacturing setup with backward integration equipped with world-class sets of equipment like Burr Oak USA and Hidaka Japan, among others. The plant set up is equipped to manufacture inverters and fixed-speed ACs along with smart AI features and heating & cooling units to cater to North India’s extreme climate. The overall manufacturing capacity is 500,000 AC units. |
![]() | Inception: 2011 Location: This factory is 300 km Northwest of North Delhi, India
This state-of-the-art manufacturing plant is equipped with highly productive, automated, and flexible lines that manufacture outdoor and indoor units of split air conditioners. Coupled with a fin and tube heat exchangers (FTHX) coil manufacturing setup with backward integration, the ACs are built with world-class equipment from Burr Oak USA and Hidaka Japan, among others. This facility also manufactures commercial split ACs, including Cassette, Mega Split and Verticool units and has a manufacturing capacity of 300,000 AC units. |
![]() | Inception: 2012 Location: Changodar, Ahmedabad, Gujarat, India Area: 9,360 sq. m. (101K sq. ft.) Products Manufactured: Deep Freezers & Chest Coolers
Located in Changodar on the Ahmedabad-Rajkot Highway in India, this cutting-edge manufacturing plant produces deep freezers with a high level of automation on the assembly line, sheet metal fabrication line, and foaming setup. With computerised control ambient Performance testing to ensure first time right product. Plant producing products as per BIS Licence for IS 7872 & BEE marking. Certified for ISO 9001, ISO 14001 & ISO 45001. |
Manufacturing Excellence
A Company-wide initiative, our Manufacturing Excellence Programme drives world-class quality, efficient production, and solutions to suit the highly diverse and extreme temperatures of Europe. This programme aligns with our core 'Customer First' value, ensuring every product reflects our commitment to excellence. Covering every aspect of our manufacturing process, this initiative fosters a robust culture where every team member plays a pivotal role.
State-of-the-art
automated factories
In-house capabilities for sheet metal and powder coating
Heat exchanger manufacturing Fin & Tube Shell & Tube DX, Flooded & Falling Film
100% testing of the product before dispatch
Strong backward integration with coil shops, fabrication establishments, paint shops and foaming setups
In-line Quality Process
![]() Overview
At Blue Star, we bring a wealth of technical expertise to the European market, honed over 80 years of industry experience. We actively contribute to shaping energy efficiency and safety standards, collaborating with industry leaders to drive innovation. Optimising Production and Quality:
Unwavering Commitment to Innovation:
| ![]() Manufacturing Processes
We implement a robust framework of Quality Assurance (QA) and Quality Control (QC) processes and continuous improvement methodologies to ensure exceptional results at every stage.
This focus on continuous improvement and quality control sets Blue Star apart. It ensures that our advanced HVAC and VRF products consistently deliver superior performance and meet customer expectations. |
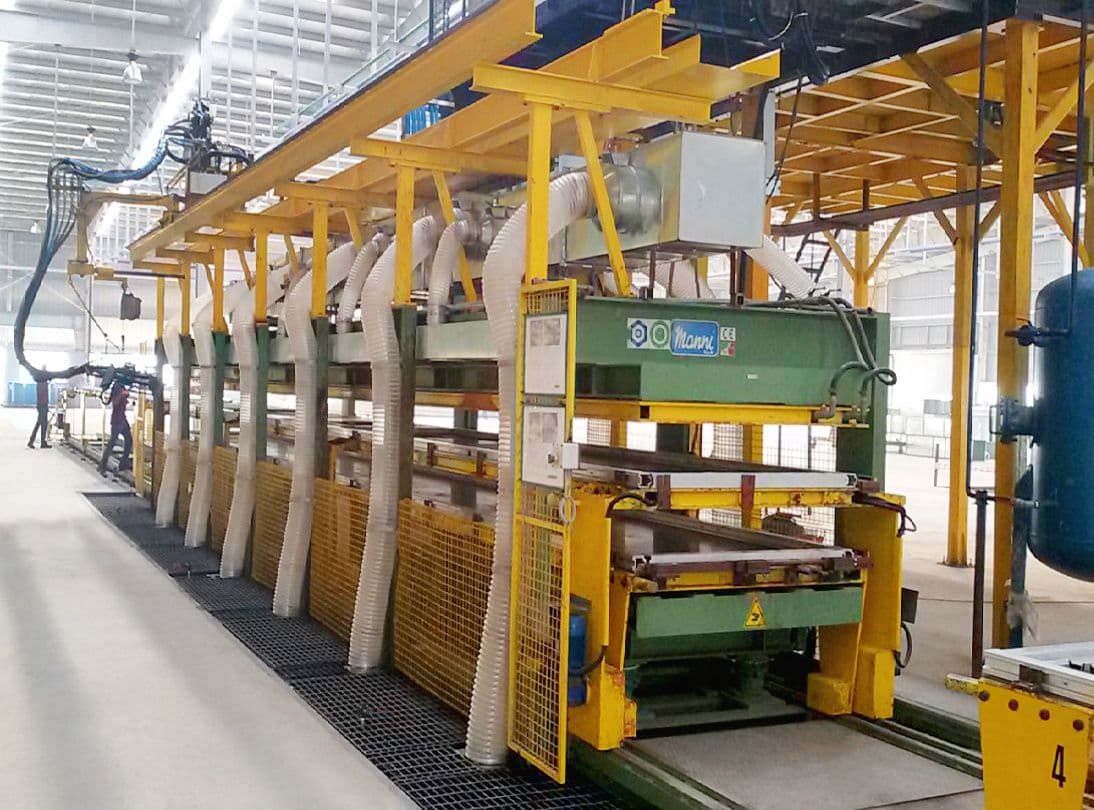
Advantages
Fully automated assembly line for 100% testing of all products before dispatch of HVAC and VRF products
Incoming component inspection
Daily verification of process parameters
Process performance tracking
A stringent 24-hour refrigerant hold, delivering leak-proof performance
Barcode traceability
Four Core Pillars
We leverage industry-leading machinery and control expertise to deliver superior product performance. This includes full load and part load tests to meet various Global Standards.
Global Partnerships Deliver Leading Technologies:
- Salvagnini (Italy): Fiber laser cutters and automated panel benders for unmatched accuracy.
- Amada (Japan): Turret punching machines for efficient sheet metal fabrication.
- Nordson (USA): Powder-coating machines with iControl technology for superior finishing.
In-House Expertise Optimises Production:
- Burr Oak Tool (USA): Advanced manufacturing methods such as setups for high-efficiency plain coils and enhanced split fins.
- S K Brazing (Korea): Automated brazing machines for superior joint strength and quality.
- Plasma cutting and automated welding: Precision in-house manufacturing of shell and tube heat exchangers.
- Micro Channel Leadership: One of the few in India with an in-house micro channel heat exchanger manufacturing line, pushing the boundaries of innovation in heater manufacturing.
Assembly-Line Innovations Our automated and conveyorised assembly lines epitomise efficiency and modernisation, primed for mass production.
| ![]()
Embracing Modern IT Tools At Blue Star, we harness the power of modern IT tools to foster productivity and ensure unparalleled product quality.
|
Sustainable Manufacturing Beyond manufacturing excellence, Blue Star is devoted to sustainability and eco-friendliness.
|
Blue Star delivers unwavering reliability and product longevity through rigorous quality assurance (QA) processes at every stage of manufacturing.
From Raw Materials to Final Dispatch:
- Meticulous testing starts with incoming raw materials.
- Stringent checks occur throughout each production stage.
- Pre-dispatch inspections guarantee every product meets our high standards.
Beyond the Basics:
- Extensive testing facilities assess product reliability, electrical safety, longevity, endurance, and environmental resilience.
- Products face rigorous challenges like UV exposure, salt spray, humidity extremes, temperature variations, and vibrations.
- Collaborations with external agencies provide additional validation of design parameters.
Blue Star stays at the forefront of efficiency and sustainability through cutting-edge HVAC manufacturing techniques and robust QA systems. We implement efficient systems at every step, minimising waste and guaranteeing consistent quality.
Driving Peak Performance:
- LEAN Manufacturing: Optimises flow, minimises waste, and boosts productivity.
- MOST Methodology: Identifies and eliminates inefficiencies through continuous improvement.
- Kaizen Culture: Over 20,000 implemented improvements foster innovation and excellence.
- Six Sigma: Maximise equipment effectiveness and drive defect-free manufacturing.
Since 1999, Kaizen has empowered teams to identify and implement improvements across all facilities.
Empowering Our Workforce
- Continuous Learning: We prioritise upskilling our HVAC manufacturing and heater manufacturing teams in the latest techniques and industry best practices, including Six Sigma, LEAN manufacturing, and soft skills. Training sessions at partner facilities worldwide keep our employees at the forefront of evolving technologies.
Safety First
- Unwavering Commitment: Employee safety is paramount. We rigorously adhere to regulations and invest in state-of-the-art safety equipment, from shop floor machine guards to aerial platforms, ensuring a secure work environment. Regular training empowers our team with first aid and firefighting skills.
Building a Strong Community
- Well-being and Camaraderie: Fostering a sense of unity, we offer opportunities for pre-work gatherings and post-work recreation, including prayer, light exercises, video sports, and games. We believe in a harmonious work environment that promotes well-being and camaraderie.
Manufacturing Journey
Beginnings in Manufacturing: Since our roots in the 1940s, making ice candy machines in Mumbai, India, Blue Star has been synonymous with HVAC manufacturing excellence. This dedication continued with the expansion of our Thane, India, factory in the 1960s.
|
Strategic Investments: While some other manufacturers in India retreated in the late 1990s in the wake of economic reforms and liberalisation, we doubled down on Blue Star manufacturing. This commitment led to the establishment of our state-of-the-art Dadra, India, factory in 1997, leveraging expertise from Rheem, USA.
|
Expanding Frontiers: Dadra's success paved the way for further expansion. Cutting-edge factories in Himachal Pradesh, Wada, and Ahmedabad, India, followed, elevating our operational standards and product quality.
|
Today, with 13 ISO 9001-2015 certified labs, Blue Star remains a leader in manufacturing. We offer a vast range of advanced and custom-designed HVAC products and are dedicated to continuously advancing our facilities, prioritising excellence, and industry leadership.
|